
Grane Mill Engine, Boiler restoration with other engines on site.
"The Steam power plant at Grane Mill is owned by the Heritage Trust for the North West on whose behalf the Grane Mill Preservation Group volunteers and associates are working to conserve and repair this unique and important heritage asset to give it the long term future it deserves."
The Preparation Area

The tape-sizer (or slasher-sizer) is the machine that combines the warping beams that come in from the spinning mills, or that have been warped from creels on site, to give the required count for the width and quality of cloth required by drawing the cotton “tapes” from several warping beams through the trough of flour or starch based size mix which was injected with steam to keep it boiling. This coating strengthened the warp yarn and minimised lint particles. The warp was then passed over steam heated drums to completely dry it before beaming perhaps a mile of warp onto a weaver’s beam to suit the loom upon which it would be woven to meet the requirement of the cloth order. Quite often a separate engine was installed in the tape-sizer room so that the tapes could be kept running whilst the main engine was stopped. Pictures to the top and right of this text show the rear and front of the tape-sizers.
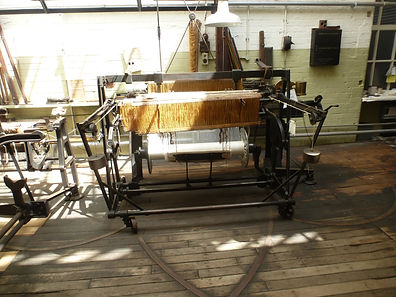
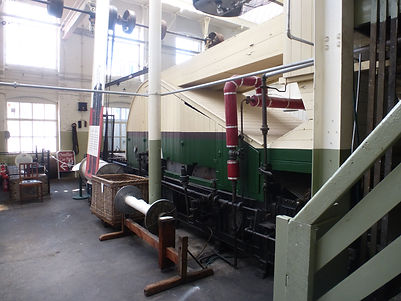
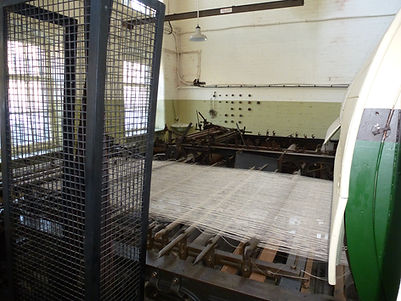

The Barber Knotter and frame was used to tie the new warp on to the end of an existing warp carefully removed from a loom that has been woven out. This was done when the new warp was the same count and weave as the previous one and saved time and minimised delays due to errors when having to draw a brand new warp through thousands of heald shaft eyes and reed dents.
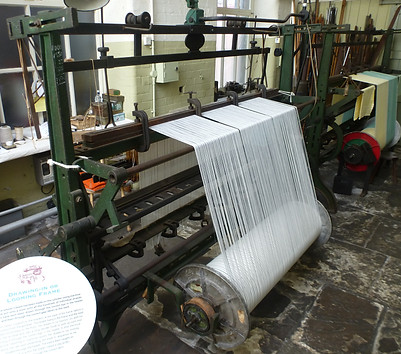
The Drawing in frame was used when you had a brand new warp that was then drawn through the set of healds and reed for putting on a loom.
A drawing of the preparation area at Grane Mill.
Click on the link to see the full floor plan of the mill and how the preparation area fits into it.
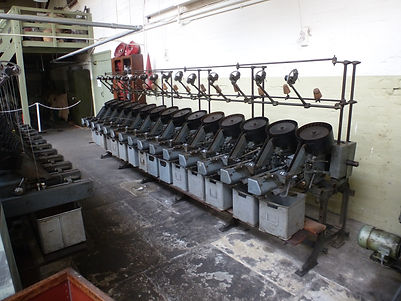
This photo shows sets of Schweiter automatic pirn winders. These re-wind spun cotton from the Spinning mills on to a standard size of pirn that suits the size of shuttle in use at a particular weaving mill for a particular set of looms.